It can often be hard to identify quality piping systems before installing. A length of Kembla Copper Tube looks and works like any other, right? All press-fittings have the same features regardless of the brand you choose? All Stainless Steel is the same in quality?
It’s often processes and technology employed during manufacture and design of products that ultimately determine their quality. Innovative processes and technology are employed in our products and is why MM Kembla products are the highest in quality and first choice for customers for so long.
Copper Tube utilising KemCore Technology
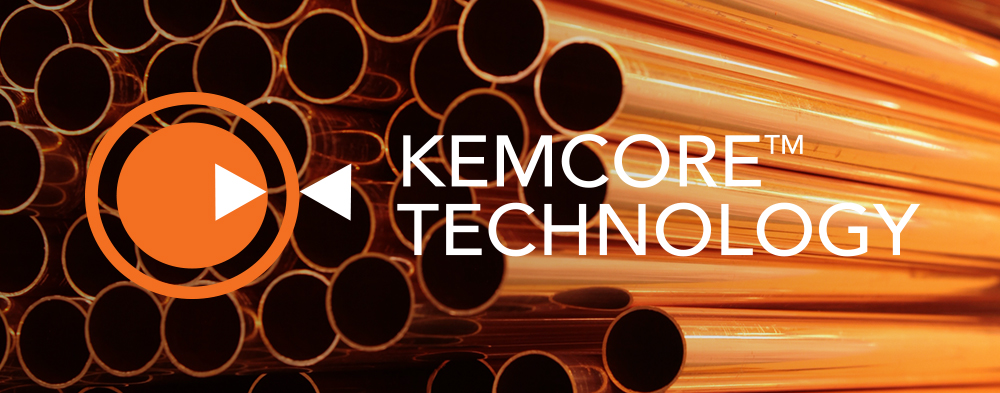
Benefits
- No weak spots
- Uniform Wall Thickness
- Optimal performance with press fittings
- Stronger Copper Tube
All copper tube produced by MM Kembla utilises MM Kembla’s very own KemCore Technology which manages and measures the eccentricity of copper tube across its entire length.
Eccentricity is the variation of tube wall thickness that occurs during the manufacture of tube. The higher the eccentricity, the more variability in wall thickness, the higher propensity for weak points on a tube and a clear sign of poor process control.
Uniform wall thickness on copper tube is particularly important when using press fittings, which applies press force and deformation of tube. Uniform wall thickness minimises weak spots and ensures optimal deformation conditions for the perfect press tight connection.
The use of KemCore technology ensures Kembla Copper Tube is the most concentric tube on the market, providing uniform wall thickness and optimal performance when used with press fittings.
KemPress – Push & Stay
Benefits
- Fitting is tight enough to complete rough in before pressing
- Fitting won’t fall off when preparing for vertical installations
- Ensures plumber has right design & tube placement prior to pressing
- Minimises risk of fitting slipping and minimum tube insertion depth not met
- Feature require the highest quality manufacturing technology and process controls
KemPress copper fittings up to DN50 and stainless steel fittings up to 50mm are equipped with the unique ‘Push & Stay’ feature.
Utlising strict process control, the tightest of manufacturing tolences and the most accurate production technology, KemPress fittings have been designed to ensure the fitting is tight enough to stay on the tube prior to pressing. Such a feature is symbolic of the high quality manufacturing and quality control processes employed during manufacture.
The Push & Stay feature has been designed to minimise risk during the installation process and make KemPress fittings easier to install.
Universal KemPress Fitting Profile
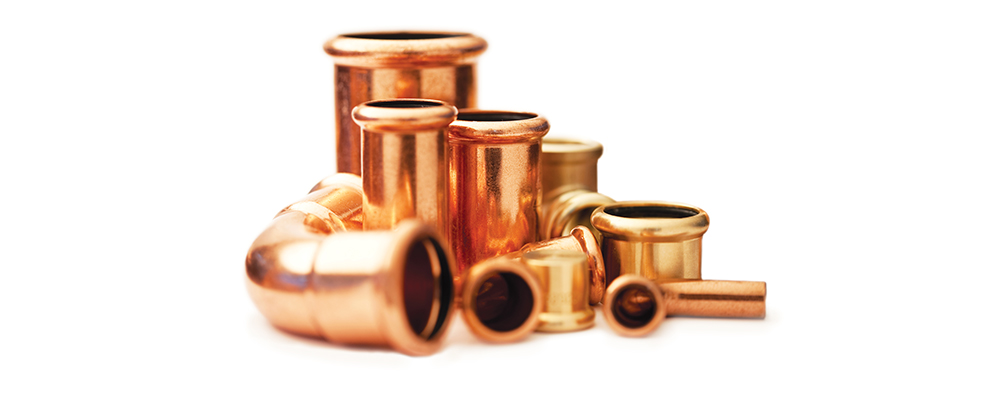
Benefits
- Copper & Copper Alloy Fittings designed to work with all compliant AS1432 copper tube in Australia
- Stainless Steel fittings designed to work with stainless steel tube compliant to
- Fitting designed to work with all press-fit tools in the market
- No additional cost of tooling for a plumber to use KemPress
KemPress fittings up to DN50 in copper and 54mm stainless steel have been specifically designed to be a universal fitting, that means it will work with all approved press-tools.
The unique SA profile means you don’t need to worry about whether a press jaw is M or V Profile, KemPress fittings are guaranteed to work with any press jaw profile and tool on the market. All you need to make sure of is that you are using the right sized press jaw.
Tools compatible and warranted for use with Kempress fittings | |
---|---|
Kempress KPS, KPL and KPL2 | Viega Picco, 4B and 5 |
Novopress ACO102, ACO202, ACO203, ECO202 and ECO204 | Ridgid RP 210-B and RP 340 |
REMS Mini=Press, Power Press & Akku-Press | Rothenberger Compact, and ROMAX 3000 & 4000 |
Milwaukee M12 7 M18 Force Logic | Klauke MAP2L NextGen |
Smart KemPress Tools – Staying fully connected
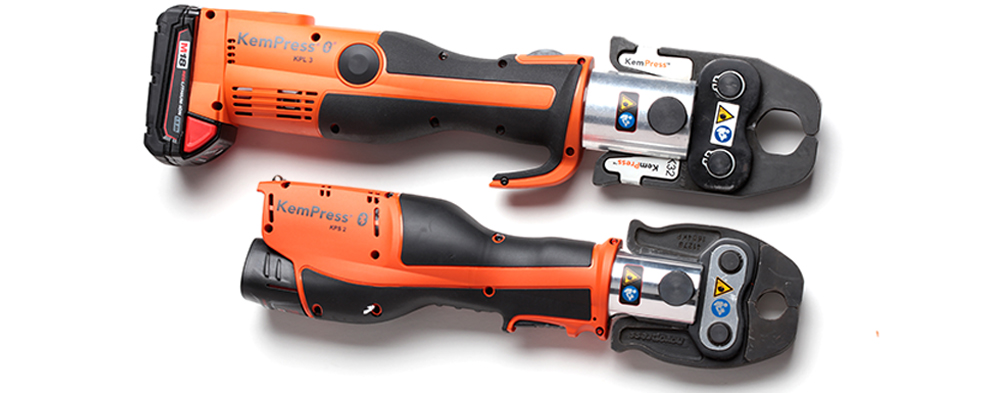
Benefits
- Full connectivity to the job site straight to you smart phone or tablet
- Press performance monitoring
- Generate site reports showing press completion data
- Detect un-pressed fittings
- Tool performance monitoring and pre-start tool check
- Maintenance of tool using service log
KemPress KPS2 and KPL3 press tools are equipped with smart Bluetooth technology so can stay fully connected with your job site and installation performance. The innovative technology combined with the Novocheck App means you can manage the job straight from your smart phone or tablet.
The ability to monitor and maintain your tool performance as well as installation performance reduces installation risk and increases the quality of your installations. Pre-start tool checks will ensure your tools are ready to work, service logs will mean you can see when your tool needs its next service and generation of site means you can detect any unpressed fittings by comparing the number of completed presses to those required on each section of work.
Download the NovoCheck App from the App Store or Google Play and connect with your tool today.
316L Stainless Steel & TIG Welding
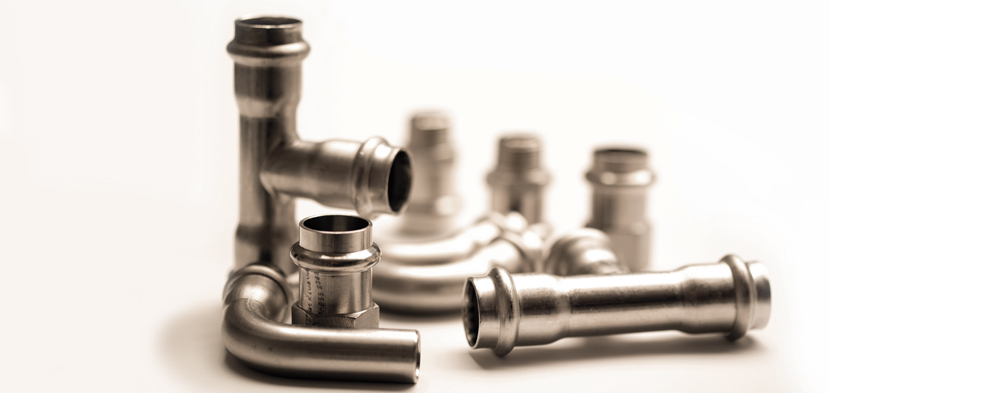
Benefits
- Better Corrosion Resistance compared to the common 316 Stainless Steel
- Less flow resistance
- Tube can be cold bent up to 28mm
- Increased resistance to stress corrosion cracking
- TIG welded for optimum press seal surface
MM Kembla Stainless Steel Tube and KemPress Stainless Steel press fittings are produced using 1.4404/AISI 316L stainless steel material. This material contains at least 2.3% molybdenum and reduced amount of carbon (<0.3%) meaning it has greater corrosion resistance compared to common 316 Stainless Steel.
All stainless steel tubes and fittings are welded using TIG welding technology, providing better control of the fitting and also the press connections. During TIG welding, tubes welded slower and in highly controlled processs which mean less stress on the tube and subsequently diameters up to 28mm can be cold bent. The TIG welding process also means the tube has a strong, mouldable seam that can be easily rolled smooth during the tube making process, creating an optimum press seal surface and reduces flow resistance internally.
A process not done by all manufacturers, all Kembla Stainless Steel fittings and tubes are fully annealed after roll forming and welding which cleans the tube, ensures a stress relieved and corrosion resistant structure and provides a correct and consistent material hardness for press fitting.